Are you trying to decide on the best material handling system for your warehouse?
Look no further!
In this blog post, we will discuss three common types of material handling: manual handling, mechanical handling, and automated handling.
We will also provide tips for deciding on the best material handling system for your warehouse, so you can choose the solution that will meet your needs and requirements.
Whether you are handling small, lightweight items or large, bulky materials, there is a material handling system that will be right for your warehouse. Check out our blog post to learn more!
What Are the 3 Types of Material Handling Systems?
Material handling refers to the movement, storage, and control of materials within a warehouse. There are various types of material handling systems used in warehouses, and each has its own unique set of advantages and disadvantages. When deciding on the best type of material handling for your company, there are many factors to consider.
The right solution will depend on your specific needs and requirements. It may even be necessary to combine two or more types of material handling to achieve the desired results. It is important to carefully evaluate all of the factors involved in order to make the best decision for your company.
There are three of the most common types of material handling used in warehouses: manual material handling, mechanical material handling, and automated material handling.
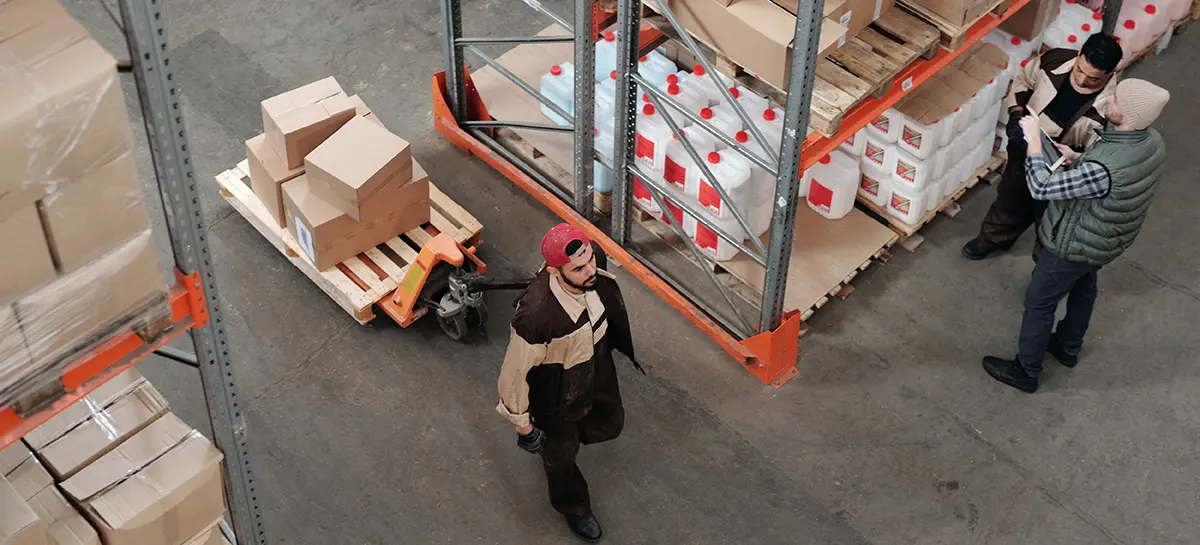
1. Manual material handling
This is the most basic form of material handling, and it involves the use of human labor to move materials within a warehouse.
This method is often used for small-scale operations or for handling lightweight materials. Manual handling can be performed using a variety of tools and equipment, such as hand trucks, pallet jacks, and forklifts.
The rise of e-commerce has led to an increase in the number of warehouses and shipping/receiving facilities. In order to save on time and costs, many of these facilities are located near transportation hubs. However, this can create a challenge when it comes to finding a workforce who live close to those transportation hubs. As a result, new solutions may be needed to address this challenge and improve the efficiency of material handling in these facilities.

2. Mechanical material handling
This type of material handling involves the use of machines and equipment to move goods within a warehouse.
Some common examples of mechanical handling equipment include conveyor belts, cranes, and hoists. This method is typically used for handling heavy or bulky materials, and it can greatly improve the efficiency and productivity of warehouse operations.
On the other hand, they can be expensive and time-consuming to install. Additionally, conveyor systems are static, meaning they are difficult and costly to move once they are in place. This lack of flexibility can be a problem when workflow changes. In such cases, the conveyor system used to move items between repair and storage would need to be scrapped or reconfigured, which can be costly and tedious.
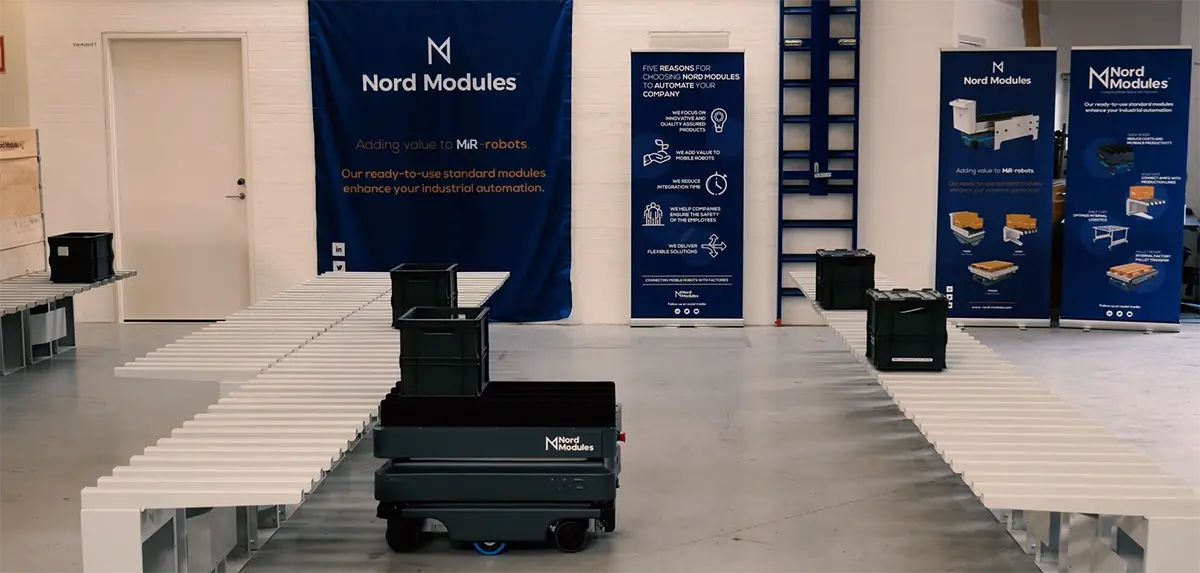
3. Automated material handling
This is the most advanced form of material handling, and it involves the use of advanced technologies like robotics.
Automated handling systems are often highly customized and tailored to the specific needs of a warehouse, and they can greatly improve the accuracy, speed, and safety of material handling operations.
One of the most common examples of automated material handling is Autonomous Mobile Robots, AMRs. AMRs can move goods in different shapes and sizes at a faster speed.
AMRs can be programmed to follow specific routes, allowing them to transport materials without human intervention. This can reduce errors and improve accuracy in the material handling process, while also lowering costs, eventually improving efficiency.
AMRs can operate safely in environments that may be dangerous to humans, such as areas with heavy machinery or hazardous materials. Additionally, AMRs are flexible and can be easily reprogrammed to handle different tasks or adapt to changing workflow needs.
AMRs can be fitted with different types of top modules to achieve the needed functionality for a surtain task. Read more about why AMRs need top modules.
Making the Right Move: Selecting the Best Material Handling System for Your Warehouse
When deciding on the best type of material handling system for your facility, there are several factors to consider, including:
- The type and size of materials being handled: Different material handling methods are better suited to different types and sizes of materials. For example, manual handling may be suitable for small, lightweight items, while mechanical handling may be better for larger, bulkier items.
- The layout and design of your warehouse: The layout and design of your warehouse can impact the feasibility and effectiveness of different material handling systems. For example, conveyor systems may work well in a warehouse with a long, straight layout, while AMRs may be more suitable for a warehouse with a complex layout.
- Your budget and available resources: The cost and resources required for different material handling systems can vary, so it is important to consider your budget and available resources when making a decision.
- Your future plans and growth potential: It is important to consider your future plans and growth potential as well. For example, if you anticipate significant growth in the near future, it may be worthwhile to invest in AMRs that can easily scale up your business. AMRs are also flexible and can adapt to changing workflow needs easily.
Don’t let the overwhelming array of material handling options weigh you down. With the right knowledge and considerations, choosing the best material handling system for your warehouse can be a smooth and successful process.
As you can see, choosing the right material handling system for your warehouse isn’t a catch-all decision. Each type of material handling system has its own unique set of advantages and disadvantages, and the right solution will depend on your specific needs and requirements.
Take the time to evaluate your needs, budget, and future plans, and you’ll be well on your way to optimizing your warehouse operations and boosting your bottom line – your warehouse operations will thank you in the long run!